Find out in the second part of our series on the semiconductor crisis.
Semiconductor Shortage: The Causes and Effects of a Monumental Event
11. November 2022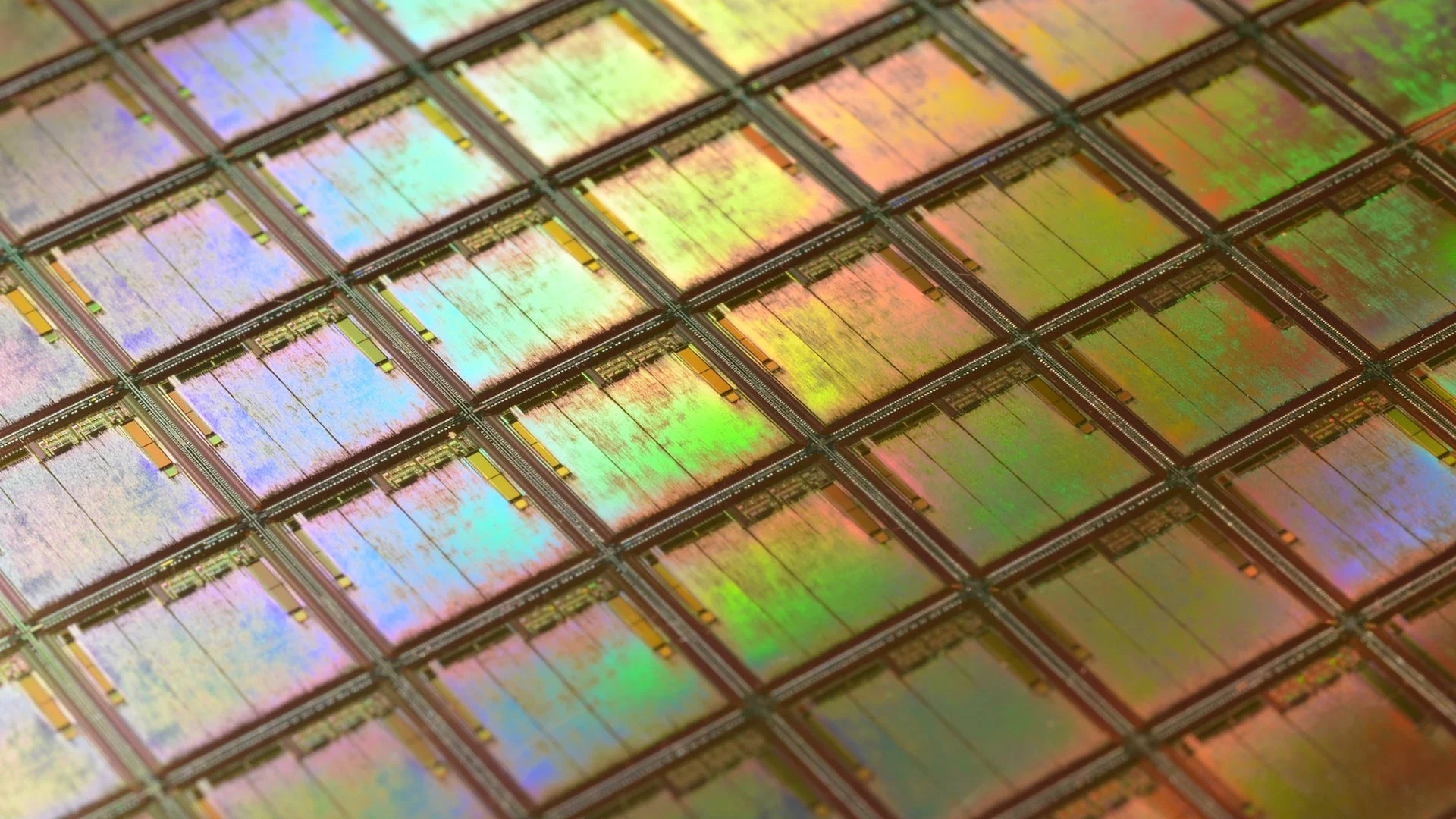
Today, nothing works without semiconductors. They are the brains behind almost everything we use in of a world that has long turned digital. But the market for these in-demand products is volatile and supply chains are as fragile as ever before. What then are the causes of the semiconductor shortage?
Nowadays, small-but-mighty semiconductors can be found in almost all electronic devices, be that toasters, smartphones, cars, or robot vacuums where they run complex processing and control operations or store data. The automobile industry relies heavily on semiconductors and the demand will continue to rise, especially with the increasing popularity of electric vehicles. The current shortage has serious consequences: In 2021 alone, 7.7 million cars could not be built as planned due to a lack of suitable semiconductors.
To understand how the current crisis came about, we must first take a look at how microchips are produced:
How are microchips made?
Microchips are manufactured on thin, round silicon wafers made out of silica sand. Through processes such as etching, lasering, and varnishing, the circuits are then created on the surface of the wafer, giving the microchip its specific function. Finally, the chips are die-cut and stored in a plastic casing for protection.
Which players are involved in the production of microchips?
The global wafer production market is largely divided among five leading manufacturers — three of whom are based in Asia. Together, they produce over 50 percent of the world’s wafers. In 2020, the Japanese manufacturer Shin-Etsu dominated a third of the market alone.
After manufacturing, wafers are processed into microchips in semiconductor factories, which are also known as fabs. These factories are also mostly located in Asia, primarily in China, Singapore, Taiwan, South Korea, and Japan. Meanwhile, the United States, with a market share of 12 percent, and Europe, with 10 percent in 2021, are far behind. This is mainly attributable to Asian manufacturing countries subsidizing the construction of new factories by 25 to 40 percent. In this respect, China seems to be the market leader.
In other words, the European economy relies heavily on imports from Asia. This makes semiconductor supply chains highly vulnerable. And this is precisely what experts identify as one of the main reasons behind the current chip crisis.
What are the geopolitical implications of the shortage?
The microchip sector is in the midst of a difficult global political climate. China and the USA are competing for market dominance in the technology market and are continually threatening to impose export restrictions. During Donald Trump’s mandate, the U.S. government had already begun to make it more difficult for China to gain access to specific technology needed for building new fabs. If the U.S. is unable to increase its microchip production, the European economy will also be impacted, as an important building block to meet the rising global demand would go missing.
And not only that: Taiwan, which currently produces over half of the global chip supply, is also dealing with a tense political situation. China sees the island state as part of its territory and repeatedly threatens it with a military invasion. Should the conflict escalate, the local economy would face disruption in supply chains and thus enormous production losses.
How does the pandemic affect the chip market?
The COVID-19 pandemic turned our world upside down, and its impact on the chip market is highly intricate.
In the spring of 2020, most companies around the world sent their staff to work from home. Many provided new devices, such as laptops, for working remotely and consumer electronics experienced a boom. This caused the demand for semiconductors to increase enormously in a very short period of time. Meanwhile, many Asian countries were experiencing strict lockdowns, which meant that goods could not be produced or shipped. In the spring of 2022, more than 200,000 containers were temporarily stuck in the port of Shanghai – one of the largest in the world. Moreover, since manufacturing companies, especially carmakers, increasingly operate on a just-in-time manufacturing model, they were unable to resort to using spare inventory. And in some areas, production came to a halt.
Why not just build new semiconductor fabs?
Shortly after the crisis began, politicians and business leaders in Europe started to call for the construction of new semiconductor factories. The goals were to meet rising demand, reduce dependence on Asian imports, and close the gap to competition from the U.S. More concretely, the EU plans to double (today’s) microchip production by 2030.
But it’s not all that simple, since building such plants is highly complex, lengthy and, above all, one thing: expensive. According to a report by the U.S. Semiconductor Industry Association (SIA), building a new fab can cost around 20 billion USD and take years. In addition, loans have become very expensive due to the turnaround in interest rates, so it is unclear whether the newly built plant will even be financially worthwhile.
Regrettably, there seems to be no light at the end of the tunnel and the current situation could become a matter of course. How then can this new normal be shaped to ensure a steady supply of semiconductors?